Consumers value convenience when deciding what products to use. Or more importantly,
Importance of Convenience in Consumer Behavior (analyticssteps.com)
“Consumers might not always be aware of the importance of convenience in their behavior until it is absent. “
I don’t know about you, but I recently left a beautiful and perfect size lunch-box on the shelf because I struggled to open it when I tried to see the inside. And I hate it when opening a product outer packaging becomes a fight between me and the cardboard or plastic around it, but love the easiness of a little pull-me tab to tear the top so my purchase magically appears.
What are some elements that make product packaging user-friendly for me?
Easy-to-Open Designs
As mentioned, being able to open the packaging without it becoming a fight or having to read thru confusing instrutions, makes the whole world when you first are presented with a product. That creates a positive first impression and contributes to overall customer satisfaction.
Unboxing videos would not be so popular would you be seeing someone tear down cardboard and dangling with scissors to break into the purchased goods. Packaging that guarantees a quick access, an organized product structure, and is not too fragile to damage by mistake is crucial for customer retention and brand loyalty.
This is not always simple, specially when it comes to fragile goods that could damage during transportation, as even if the immediate product packaging may be friendly, the outer package could be a total nightmare. Therefore, manufacturers must consider the strength and integrity of the packaging to prevent accidental opening during transportation and storage while ensuring that end-users can open it effortlessly, which proves to be difficult to achieve sometimes.
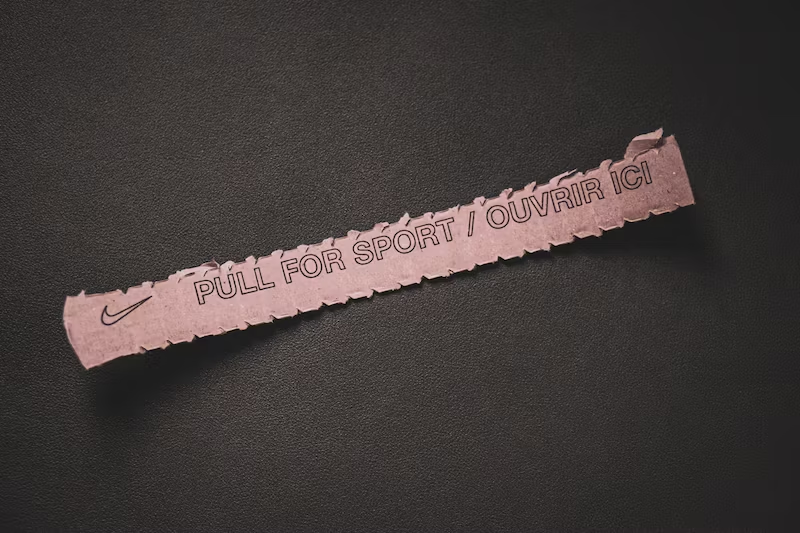
Some elements that you may consider to make your packaging easy to open are:
- Tear strips and perforations
- Pull tabs or finger lifts
- Textured or embossed easy-grip features
- Easy-to-peel seals, such as peel-off stickers or tape
- Push-button releases
Resealable packaging
Packaging that cannot be resealed often means that consumers need to use other materials to reseal your product, or need to use a different container for it once opened, which defeats all your branding efforts.
Some products require to be re-sealed after each use, to preserve freshness or to prevent spills like personal care items, pet supplies, and household cleaners. Following in the convenience clause, your clients would appreciate being able to reseal the package without having to transfer the contents into additional containers.
Incorporate resealable closures, such as zippers, snaps, adhesive or magnetic strips; This allows users to open and close the packaging multiple times without compromising its integrity!
But this is easier said than done, as effective resealable packaging requires careful material selection and design considerations to maintain the integrity of the seal and prevent leakage, which also goes hand in hand with regulations about product safety or that increase the risk of tampering.
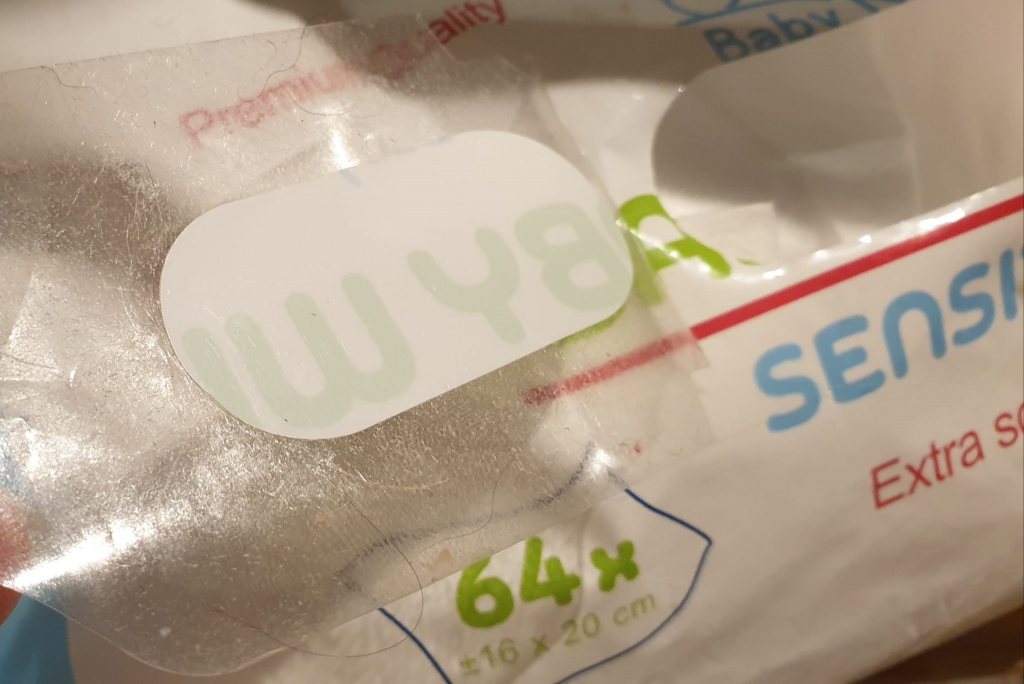
Additionally, manufacturers must conduct rigorous testing to ensure the resealing mechanism functions as intended throughout the product’s lifespan – this is not always the case when the re-seal gets in contact with “the elements” around it.
This often means that good resealing options come with a cost, and this is why they are not used YET on so many of the daily need products, but we start to see these in luxury or non-essential products. The trend is there, and as long as research continues and there is investigation into new ways of resealing products, and maybe some regulations come in to place, we will see these spread to essential products in due time.
Ergonomics
Ergonomics play a crucial role in user-friendly packaging, especially for products that consumers handle regularly or for extended periods. For example, in personal care products or household tools, ergonomic packaging reduces strain on users’ hands and provides a comfortable grip, enhancing the overall user experience. This is why ergonomic packaging will not only enhances the user experience but also demonstrates a brand’s commitment to customer satisfaction and well-being, making it a reason for staying loyal to a brand or product.
Manufacturers must carefully assess the target audience’s needs and preferences when designing ergonomic packaging. Conducting user testing and incorporating feedback during the design process can lead to packaging that aligns with consumers’ physical requirements and enhances usability.
Some ideas of ergonomic packaging that you can incorporate into your packaging
- Soft-touch surfaces or materials, that enhance the tactile experience, and making the product comfortable to handle.
- Curved edges and corners that make the packaging safer to handle.
- Grip indentations that help handle the packaging securely and comfortably
- Packaging that can be opened, closed, or dispensed with just one hand
- Include handles into your packaging for easier handling and weight distribution
What are some innovations that you are carrying into your packaging design to make sure that it ticks all the boxes for convenience for your target group? How are you incorporating feedback from them into your design efforts? And finally, how are you making sure that the packaging meets all the regulations and brand requirements when it comes to these user-friendly elements?
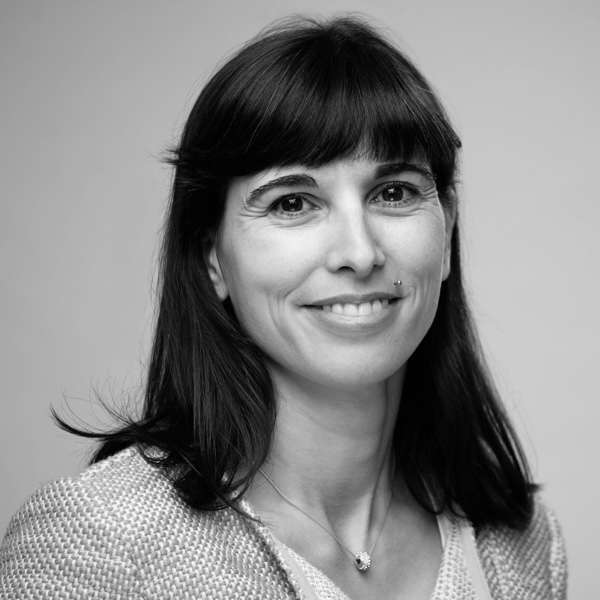
Marketing